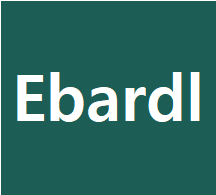
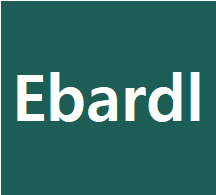
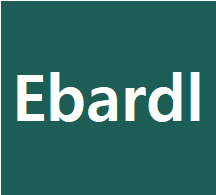
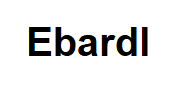
A leading company in prototyping & tooling production technology
- …
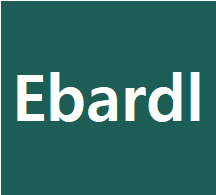
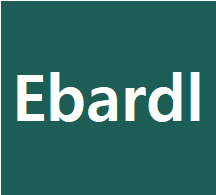
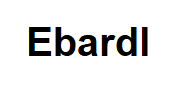
A leading company in prototyping & tooling production technology
- …
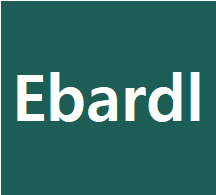
What is Precision Tube production processing?
Precision Tube Production is a detailed process that requires multiple steps to create tubes with exact dimensions and smooth surfaces. Here's a general breakdown of how it works:
Material Selection: The process begins with the selection of the appropriate metal or alloy based on the requirements of the final application.
Tube Formation: The selected material, typically in the form of a flat strip, is then formed into a cylindrical shape using a series of rollers in a process known as tube forming or tube rolling.
Welding: Once the material is formed into a tube, a high-frequency electric current is used to heat the edges, causing them to fuse together in a process known as Electric Resistance Welding (ERW). This creates a continuous, seamless tube.
Cold Drawing or Pilgering: The tube then undergoes further processing to refine its dimensions and improve its mechanical properties. Cold drawing involves pulling the tube through a die to reduce its diameter and wall thickness. Pilgering, on the other hand, involves compressing the tube's diameter and wall thickness simultaneously.
Heat Treatment: After cold drawing or pilgering, the tubes often undergo heat treatment. This process relieves stresses caused by forming and welding, and also improves the tube's mechanical properties.
Finishing Processes: Additional finishing processes may be carried out to improve the tube's surface finish, such as polishing or coating.
Inspection and Testing: The final step in Precision Tube Production is inspection and testing. This ensures that the tubes meet all the required specifications for dimensions, surface finish, and mechanical properties.
The result is a high-quality tube that is used in a variety of industries where precision and reliability are paramount, such as in the automotive, aerospace, medical, and energy sectors.