Blackening treatment involves heating and oxidizing metal workpieces in a solution of concentrated alkali and sodium nitrite. This process creates a uniform, dense layer of magnetite (Fe3O4) on the surface, approximately 0.5 to 1.0 micrometers thick. This layer not only adheres firmly to the metal but also serves as a reservoir for oil, enhancing the rust resistance of the workpiece. Essentially, blackening is an oxidation process of the metal surface, resulting in a blue-black color. As the thickness of the oxide layer increases, the color transitions from colorless to yellow, orange, red, purple-red, purple, blue, and finally black.
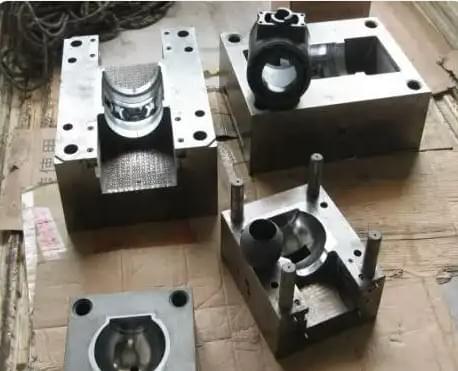
The overall heat treatment process does not significantly affect the oxidation of the workpiece. However, chemical heat treatments have a considerable impact on subsequent blackening.
After soft nitriding, the surface contains nitride or nitrogen-rich ferrite structures. These structures have a lower electrochemical potential, making oxidation difficult, which slows down the oxidation rate. Consequently, the blackening process may leave uncoated areas. To address this, two solutions are recommended:
.
- Carbon tool steel and general alloy steel turn black to blue-black after treatment.
Workpieces that undergo carbonitriding face similar challenges to those of soft nitriding. In addition to the solutions for soft nitriding, it is advisable to reduce the ammonia supply and lower the nitriding concentration during carbonitriding quenching. Additionally, control the residual austenite content in the carburized layer.
Nitrided workpieces have excellent surface corrosion resistance, making blackening very difficult and generally unnecessary.
The chemical composition of steel affects the color of the oxide layer as follows:
- Carbon tool steel and general alloy steel turn black to blue-black after treatment.
- Cr-Si steel turns reddish-brown to brown-black, such as 60Si2Mn, which appears reddish-brown after blackening.
- High-speed steel turns brown to dark brown.
- Cast iron turns purple-brown to black-brown.n.